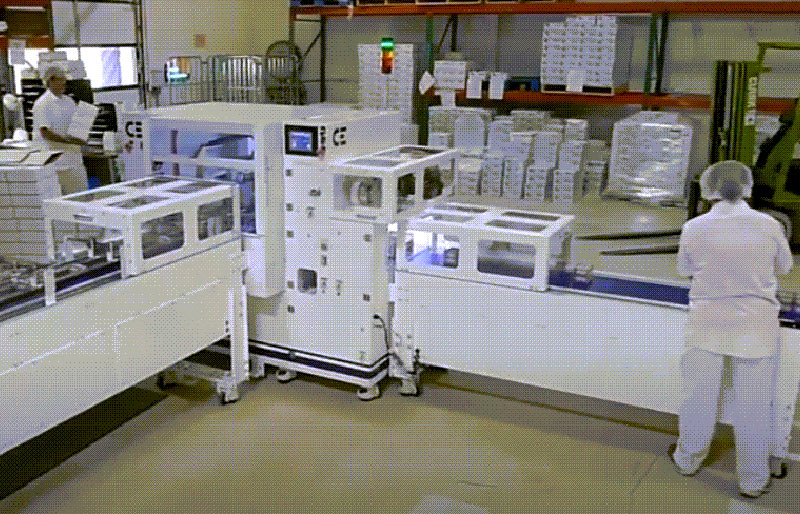
The Prescription for Low Packaging Productivity
HOW SUPPLYONE IMPROVED PACKAGING LINE PRODUCTIVITY BY 25% THROUGH STACKING AND BANDING AUTOMATION
WHO
A privately held manufacturer of OTC branded and private label products operating as both a primary and secondary packager for distributing pharmaceuticals to national and regional chains, food and grocery stores, drug wholesalers, co-ops and independent pharmacies throughout the United States.
THE PROBLEM
The pharmaceutical company’s secondary packaging line had recently been almost fully automated. But toward the end of the line, finished product bundling and shrink-wrapping was still done manually. As a result the company was experiencing low productivity, inconsistent bundle quantities and staffing pains
Bottlenecked productivity/throughput
The OTC and healthcare manufacturer’s packaging and distribution operation was suffering from low productivity. They were experiencing a bottleneck in the manual carton stacking component that sat downstream of a fully-automated primary packaging line. Here, a two- to three-person team was responsible for receiving finished cartons and bundling various configurations to be shrink-wrapped and prepared for distribution.
The fully-automated primary packaging line was processing products at a rate that human personnel simply couldn’t keep up with: upwards of 18,000 to 20,000 units a day. This resulted in frustrating and costly downtime and forced the line to slow to 60% to 70% of its full capacity to accommodate the bottleneck.
Inconsistent bundle quality
In addition to slowing the down the line and hurting productivity, the bottleneck at the bundling stage was also degrading the consistency and quality of the packages. Each bundle was oriented, stacked, and banded by a human technician. This manual bundling was impairing the otherwise near-perfect packages the automated machines were producing upstream.
The threat of understaffing on a high-throughput line
Expecting to raise the bar on packaging productivity given the opportunities unlocked by automation upstream, those areas that remained manually operated took on a whole new level of risk given the everyday threat of illness, position changes, and other staffing problems that could affect the line.
Staffing levels of two to six personnel had to be maintained depending on the product on the line. When the line went understaffed, it meant a further reduction in productivity. This issue rippled through the business and the supply chain they maintain with customers all over the country.
HOW WE SOLVED IT
After an initial search for an automated stacker and bander came up empty, the Operations Manager assumed the only option was to build a custom solution. This, of course, would be difficult, slow, and expensive, without any guarantee of success once it was in place.
That’s when SupplyOne’s Mark Dobransky, Director, Packaging Automation introduced the manufacturer to Dan Odegard of Madison Banders. Mark and Dan assessed the challenge and recommended the Controls Engineering’s Array Pack, an automated stacker and bander that integrates seamlessly with most packaging lines and is capable of keeping up with the high throughput of today’s automated packagers.
The Array Pack AP-25 fully automates carton stacking, indexing, and banding for vertical and horizontal stacked cartons and combined configurations, and integrates with carton filling equipment for a seamless packaging flow. Bundle integrity is enhanced through Reactive Tension Control that automatically adjusts to varying product sizes and shapes while allowing the operations to finitely control the bundle tension.
The Operations Manager of the OTC and healthcare manufacturer quickly decided to implement the Array Pack stacking and banding solution. The AP-25 effectively eliminated the bottleneck and further automated the manufacturer’s secondary packaging line.
WHY THE CUSTOMER IS SMILING
The company’s Operation Manager notes significant benefits resulting from the Array Pak solution including less labor costs, higher productivity, and more satisfied customers.
50% reduction in labor costs
Simply by adding the Array Pack to their line, the company was able to reassign half the labor required to staff their line.
“Almost immediately, we were able to reassign positions and reduce staff on our line from four people down to two. In some instances, we’ve taken it from six people down to three, depending on the job that we’re running. So, that’s been huge for us.”
20% to 25% increase in throughput productivity
Once the Array Pack was fully integrated into its secondary packaging line, the bottleneck evaporated, allowing the company to realize the full potential of the automation investments it had put in place.
“We had a line that was operating somewhere between 60% and 70% throughput. And we’ve already taken that all the way up to about 80% to 85%. It’s certainly increased our productivity.”
Fast, easy configurability
With a variety of change-out parts provided as part of every installation, the manufacturer’s frontline technicians can save each configurability setting it uses across its various product lines directly into the machine. This enables technicians to save time switching over—minimizing downtime.
“The configurability is great. It’s just a couple change-out parts and then changing the setting. It takes very little time and our basic technicians can do it with ease. That time savings really adds up as we grow and add more products to the line.”
Higher consistency and end-user satisfaction
While tough to quantify, the company reports a more consistent, user-friendly bundle from the Array Pack compared to the typical manual bundle—an advantage that reflects well on end-users at the end of the supply chain.
“The bundles are more consistent and definitely improved aesthetically. They’re just nicer to look at and handle. Without the human element, the cartons are being oriented one way, and one way only. When our customers get our packages, you know that it’s a lot cleaner, they’re a lot neater, a little more consistent. That might seem like a small detail, but it’s important to us because it’s really important to them.”
Following their first Array Pack installation, the immediate impact and sustained improvement in productivity prompted the company to procure two additional machines in an effort to reach higher productivity levels on other lines as well.
Ready to maximize your packaging productivity and efficiency?
Schedule a consultation with a SupplyOne Packaging Automation Specialist.