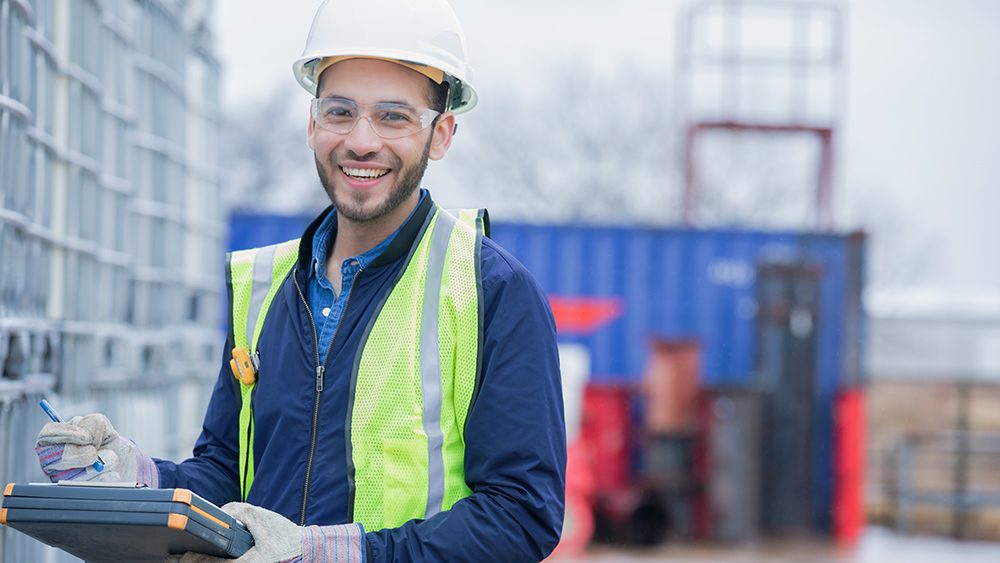
Improved Inventory Management for a Chemical Manufacturer
VENDOR CONSOLIDATION LEADS TO BETTER PROTECTION AND $24,000 IN WORKING CAPITAL
WHO
One of North America’s largest independent manufacturers of household, pool, auto, and personal care chemicals retailing through home improvement, hardware, and pool chemical distributors nationally.
THE PROBLEM
The customer had an extensive campus as well as seven manufacturing facilities, and two storage and distribution facilities.
Warehousing and purchasing efficiency were a challenge, and pressure mounted for the headquarters team to reduce costs. Each plant would requisition safety products that included garments, respirators, gloves, hearing protection, and more, multiple times per week based upon their unique needs and production schedules.
HOW WE SOLVED IT
SupplyOne worked with purchasing and the storeroom personnel to evaluate the labor requirements each week to process orders for each of their plants. Certified Packaging Specialists conducted a safety supplies audit and assessment to determine where savings might be realized through vendor consolidation.
SupplyOne recommended the Freedom RFID inventory control system utilizing barcoding technology to reduce the time and labor required to process safety requisitions each week. We suggested that each plant manager, or their approved go-to person, order safety items once per week, and instituted summary billing to consolidate their invoices.
Additionally, SupplyOne placed consignment safety inventory into a container in the storeroom to increase product availability and eliminate stock-outs. Further savings and safety improvements were realized by consolidating the disposable garments and gloves the company purchased through another, well-known brand.
WHY THE CUSTOMER IS SMILING
The initial study showed that the Freedom RFID system resulted in labor savings of over 39 hours each week, allowing the people responsible for the task to redeploy their efforts to more value-added activities elsewhere in the department.
Summary billing condensed the company’s accounts payables processing costs and labor required, reducing the number of invoices per month from 60 to 9.
The consignment inventory freed up approximately $24,000 of working capital. To top it off, , the vendor consolidation resulted in better protection for their employees and it reduced their overall spend by more than $54,000 annually.